鉄鉱石を水素で還元し、H2Oを発生させることで、CO2の排出を削減。
水素還元によるメリット
通常、COガスを用いて鉄鉱石を還元*するとCO
2ガスが発生します。しかし、水素を用いて還元するとH2Oが発生するだけでCO
2は発生しません。従って、水素を用いる鉄鉱石還元法は、地球に優しい製鉄法と言えます。また、水素ガスによる還元速度は、COガスを用いた場合よりも5倍も速いのです。
*鉄鉱石中の酸素は鉄の原子と化学的に結合しており、その酸素を他の元素で鉄から切り離すことをいいます。
日本の高炉では、一部石ころ状の鉄鉱石も使用しますが、殆どの鉄鉱石は粉状なので、このままで高炉に装入するとガスの通路がふさがれてしまいます。そこで高炉の中で砕けてしまわないように、一旦焼き固め、焼結鉱として強度を持たせて高炉に装入します。下の写真にあるように、焼結鉱には100~500ミクロンの細孔があり、この中を還元ガス(COあるいはH2ガス)が通って焼結鉱の内部に侵入し、焼結鉱細孔内壁表面、および、さらに鉱石内部のより微細な組織に侵入し、還元反応を起こします。
焼結鉱とその内部の細孔写真
化学反応が起こる界面
従来の高炉製鉄法では鉄鉱石中の酸素を除去(=還元)するのに、COガスを利用しています。
COガスは分子のサイズが大きいために、鉄鉱石中の内部まで浸透することが困難でした。
H2ガスは分子のサイズが極めて小さいため、容易に鉄鉱石内部まで浸透していくことができ、その浸透速度はCOガスの約5倍とも言われています。よって、H2を高炉で用いることにより急速な還元が可能です。
※図を拡大して見ることができます。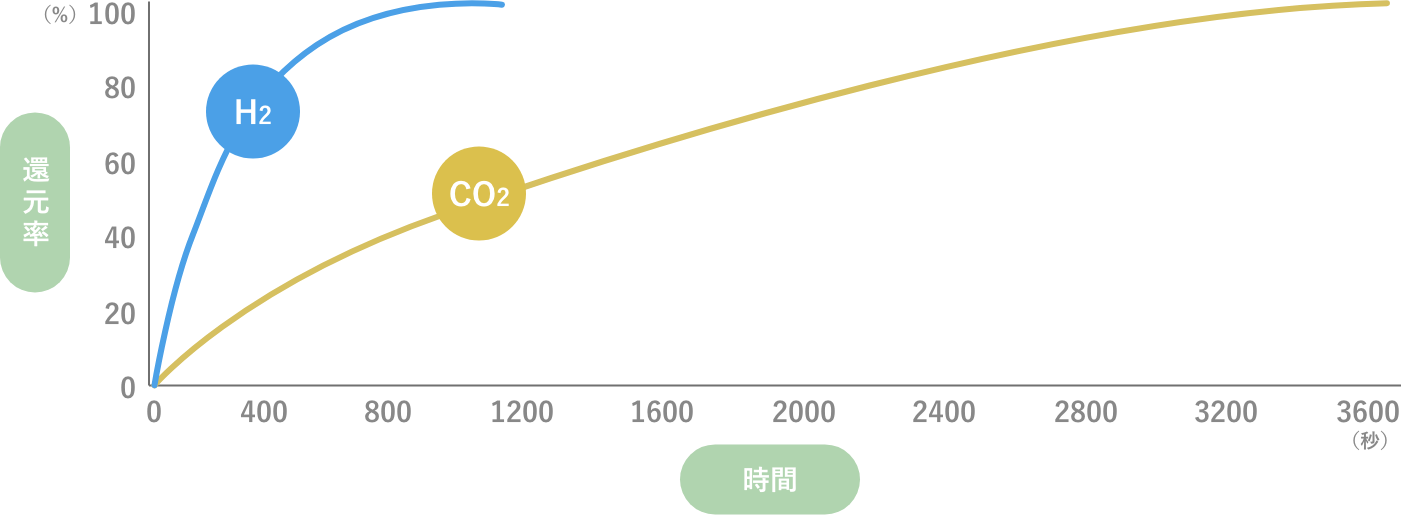
COURSE 50高炉におけるCO2削減方法
酸化鉄の還元反応には3つの形態(CO還元、水素還元、直接還元)があります。これらのうち直接還元は非常に大きな吸熱反応です。通常の高炉では、COガス間接還元、水素ガス間接還元、炭素直接還元の割合が6:1:3程度で反応が進行しています。高炉の長い歴史の中で発熱反応であるCOガス間接還元の割合を増やすことにより炭素直接還元の割合を減らす努力がなされてきましたが、現在は既に熱力学的な限界に近い条件で操業がなされており、現状レベルから抜本的にCO
2を削減することは困難であることがわかっています。
そこで、COURSE50プロジェクトでは、炭素直接還元よりはずっと小さな吸熱反応である水素還元を促進することによって炭素直接還元の割合を低減し、高炉全体として還元に必要な熱量を低減することによって、10%以上のCO2削減を目標としています。COURSE50高炉では、製鉄所内で発生するCOG(コークス炉ガス)に加え、将来的に調達可能量が増加すると見込まれる外部からの水素ガスを活用して水素還元を促進するとともに原料の反応性を適切に制御したり、高炉から排出されるガスからCO2、H2Oを分離除去し還元能力を再生したガスを循環して再利用することにより、CO2削減を狙っています。
※図を拡大して見ることができます。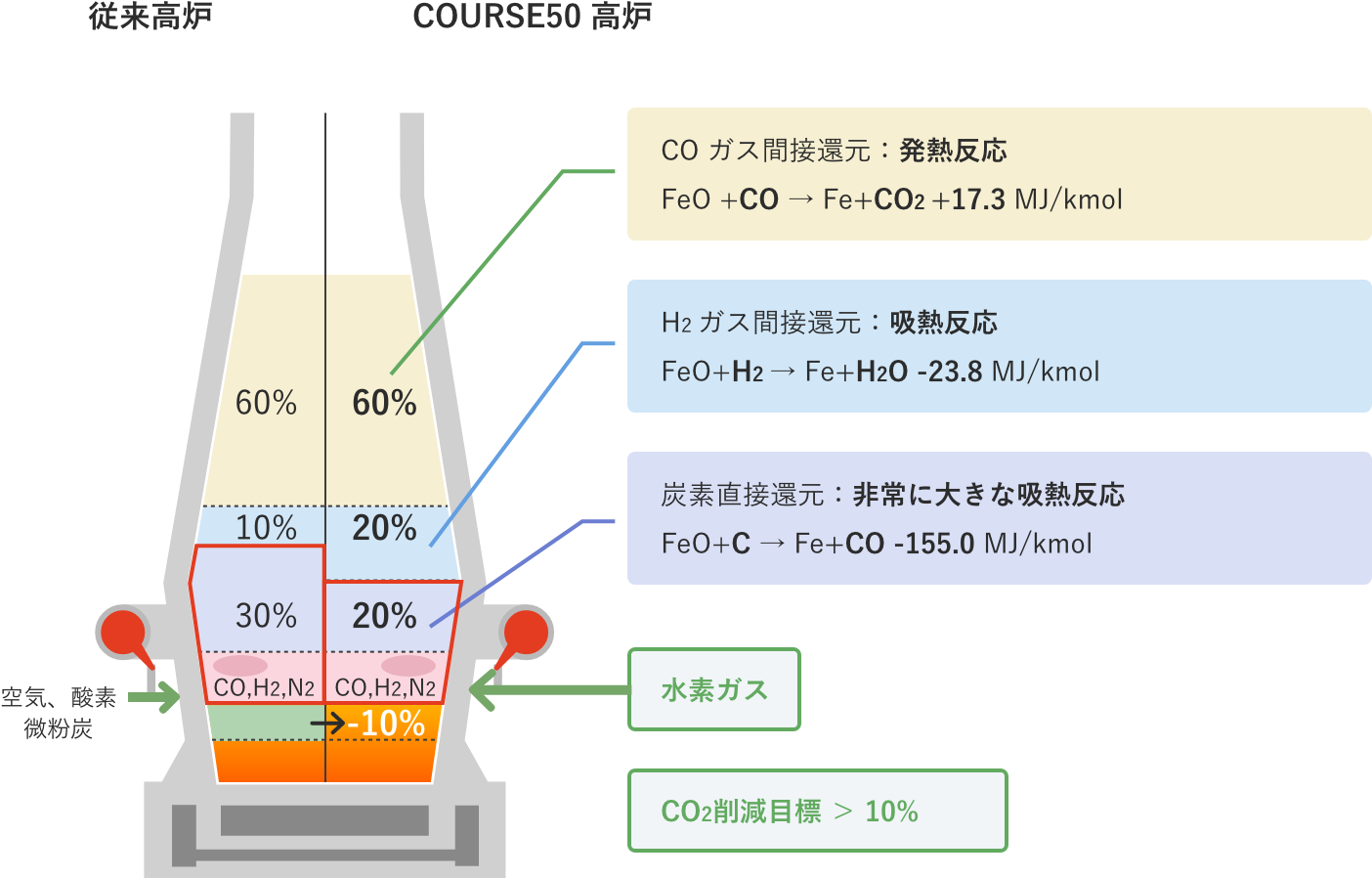

実験高炉を用いた実証実験
試験高炉は高さ約20m、内容積12m3(国内主要高炉の約1/400、写真左奥の青い建物の中に入っています)で、2015年9月に完成しました。2回の熱間試運転の後、2016年からほぼ2回/年の試験操業を実施し、2021年1月現在まで合計9回実施しています。1回の操業は約30日で、約40人のメンバーが四直三交替で24時間試験に従事します。操業中は、試験高炉上部から鉄の原料である塊鉱石と焼結鉱、還元材であるコークスを交互に装入すると共に、試験高炉下部にある三本の羽口から、約1000℃に加熱した空気と酸素、75μm以下に破砕した石炭(微粉炭)、そして水素を含んだ還元ガスを連続で吹き込んで、塊鉱石と焼結鉱を還元します。そして2時間に1回、約1450℃の銑鉄(溶けた鉄)とスラグ(鉄源原料中の鉄以外の有用物)を合計約4,000kg、炉底にある出銑口から抜き取ります。これを約30日間連続で行いながら、高炉で消費されるカーボン量に関わる様々なデータを採取します。
水素還元技術の現状
世界的には、天然ガスを用いた直接製鉄法(鉄鉱石から固体還元鉄を直接製造する方法)が稼動しています。
日本は天然ガスに乏しいため、直接製鉄法による生産を行っている企業は国内にありません。また、コスト競争力のあるレベルでH2を製造することが困難なことから、高炉製鉄法でH2を用いる技術はこれまでにありませんでした。COURSE50では、水素還元の実現に向けての技術課題を乗り越えるための挑戦を行っています。